Cleaning Support for Regeneration
We provide services of removing films attached to shield parts and internal jigs incorporated in equipments as well as adjusting surface coarseness and correcting or repairing parts. Regenerated parts are delivered in a state where they can be used immediately after delivery. Our regeneration by cleaning, which has acquired ISO-9001 international quality certification, enjoys a high reputation among many users. We will do our best to keep providing you with high-quality and low-cost services.
Features of our Cleaning support
- We promptly collect items to be cleaned, using the most appropriate transportation equipment for your systems.
- We use our wealth of experience in the vacuum industry to resolve your problems.
- Cleaning and packing are done in the clean state based on our extensive know-how of semiconductors.
- Quality control and cleaning are performed under a control equipment conforming to ISO-9001.
- You can place an order for regeneration by cleaning just by checking items to be cleaned on the check.
System
- Sputtering equipment
- Etching quipment
- Deposition equipment
- ECR equipment
- Plasma CVD equipment
- Other vacuum equipment
Parts
- Protective shield
- Substrate holder
- Trays
- Shutter
- Protective plate
- Quartz parts
- Wafer gripper
- Electrode plate
- Other vacuum parts
What is "Cleaning"?
Cleaning is a surface processing technique that removes piled/adhered film and microscopic particles in vacuum chamber, and reduces to occurring particles that gives minute pattern bad influences.
Cleaning process
1. Acceptance check | Quality of attached films, quantity, feasibility of regeneration, contents of specification, etc. are checked. |
---|---|
2. Process of peeling off attached | Since the optimum working method is selected depending on the quality of attached films and the type of base materials, deterioration of parts is minimized (effective for repetitive use of parts). |
3. Wet process / Dry process | By immersing parts in acid or alkaline solution in a cleaning chamber provided with wastewater processing facilities, attached films are peeled off. Irregularities of peeling can be eliminated by using blasting or a thermal spraying device, while achieving uniform coarseness of the surface for improved film adhesion. |
4. Finishing | Attached films are peeled off mainly with an automatic blasting device and robot. |
5. Correction and repair | Presence of distortion (such as curling and deformation) is checked, and corrected if any. Damaged parts are repaired to restore the initial state according to the manufacturing drawing. If the initial state cannot be restored, new parts will be manufactured with the consent of the customer. |
6. Check | Dimensions, distortion, surface coarseness, tapped holes, etc. are checked item by item in the most appropriate way for each part. |
7. Degreasing | Automatic water precision cleaning:Ultrasonic cleaning is performed with an automatic cleaner using water-soluble solvent. Automatic ultrapure water precision cleaning:Ultrasonic cleaning with ultrapure water minimizes generation of particles. |
8. Vacuum drying by heating | Parts are set to the vacuum heat-drying furnace (with cry pump) and dried by heating. Since less gas is generated from the surface of parts dried by vacuum heating, startup time after maintenance can be minimized. |
9. Final check | The product is inspected according to the standard to make sure that the desired quality is achieved. |
10. Packing | Cleaned parts are double-packed in antistatic polyethylene bags and air-cap wrapping, and then packed in a dedicated plastic case with plenty of cushioning materials. |
11. Delivery | Precision parts after cleaning are quickly returned to you in pristine condition. |
What is Thermal spraying?
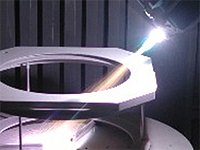
Thermal spraying is a surface processing technique that heats materials to be sprayed using a heating source, and sprays them in the melted state onto parts, thus forming a film on the surface.
Purpose of Thermal spraying
The purpose of thermal spraying during cleaning for regeneration is to prevent peeling of deposited films by making the surface of shield parts more coarse, while absorbing stresses applied to deposited films by thermal cycles, making the most of the flexibility of films.
Features of Thermal spraying
- Peeling tends not to occur even with films subject to large internal stress (generated by sputtering or CVD).
- Little damage occurs to base materials during cleaning for regeneration, thereby extending the service life of shield parts.
- Particle quantity is kept stable at a low level.
- The time until particle out-of-specification occurs is extended.
The following functions can be added by thermal spraying
- Abrasion resistance
- Heat resistance
- Corrosion resistance
- Insulation resistance
Plasma spraying

From among numerous available spraying methods, we have chosen plasma spraying, as it has superior flexibility, little porosity, and high selectivity of spraying materials.